Research Methodologies
Consistent mechanical models for the analysis and design of concrete structures, were the main research focus of the predecessor at the chair of concrete structures, Prof. P. Marti (1990-2014), who established a multitude of extremely useful consistent mechanical models. We strive to continue this tradition. First results include the generalisation of compression field models to fibre and hybrid reinforced concrete and a unified mechanical model for partial area loading, combining the effects of active, passive and geometrical confinement.
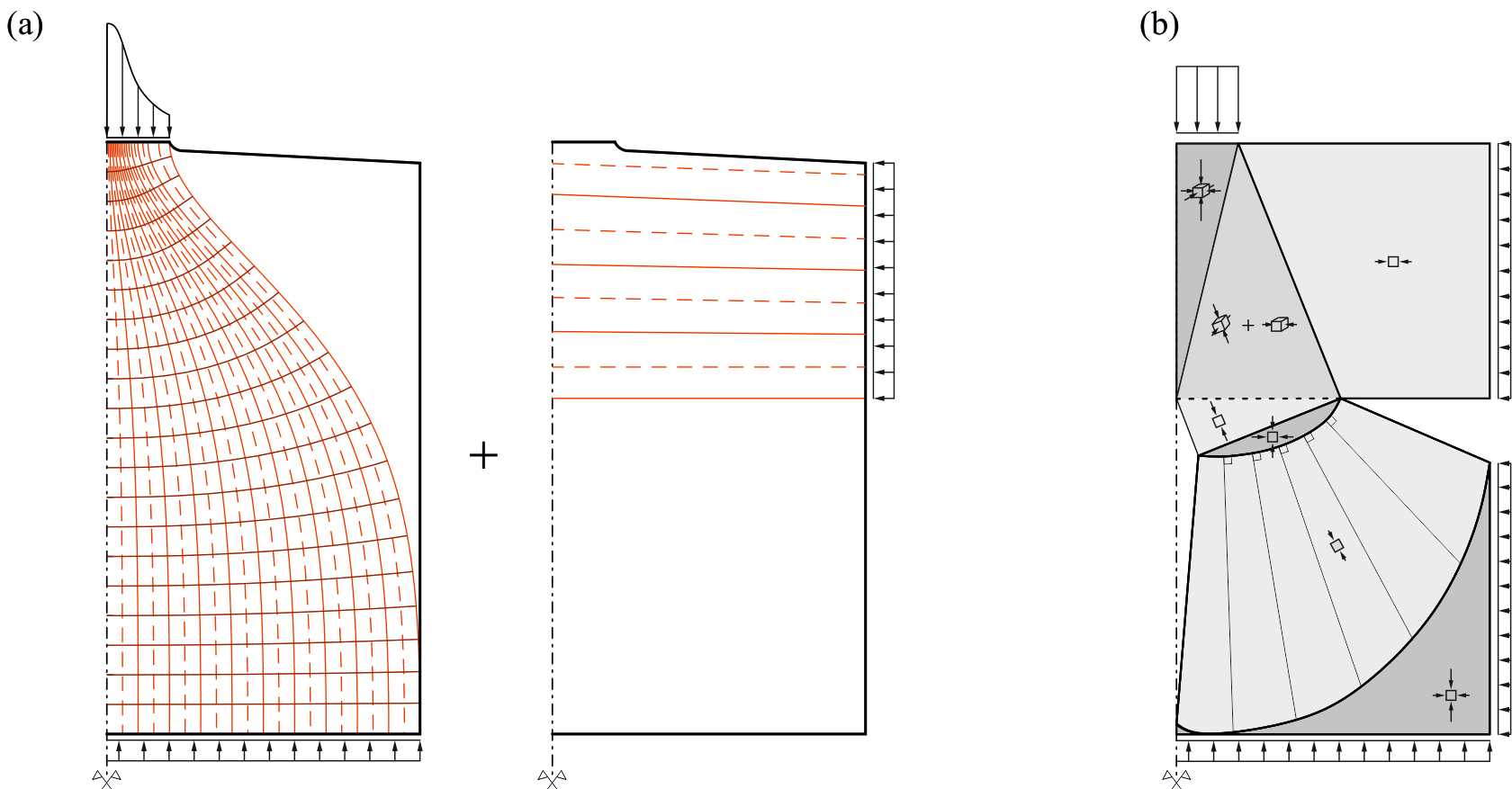

Large-scale testing has a long-standing tradition at the Institute of Structural Engineering. In 2017, we enhanced the institute’s facilities for large scale structural testing with the Large Universal Shell Element Tester (LUSET), a worldwide unique research facility that our group conceived, designed, procured and commissioned in-house with the support of IBK’s structural lab manager. This innovative testing facility is extremely valuable particularly for investigating the load-deformation behaviour of concrete plate and shell elements, a key research question in the field of future-oriented structures. In order to maximise the benefit of experiments in LUSET, we are using cutting-edge instrumentation including (i) full field 3D digital image correlation measurements on both faces and (ii) distributed fibre-optical strain measurements based on Rayleigh backscatter analysis, with optical fibres glued along the reinforcing bars. The image correlation measurements are processed using an automated crack detection and measurement algorithm developed by our group and combined with the fibre-optical strain measurements, yielding extremely valuable insight into the mechanical behaviour of the test specimens without affecting the behaviour by the measurements.
Numerical models capable of accurately predicting the behaviour of structural concrete elements subjected to arbitrary loading are becoming ever more relevant, both in research as well as industry. While powerful nonlinear finite element packages for the analysis of concrete structures are available today, these programs are of limited use to structural engineers since they require material parameters unknown at the design stage and, more importantly, account for the tensile strength of concrete, which is incompatible with the design philosophy of modern design codes. Here, our goal is to implement the mechanically consistent models developed at our chair (by ourselves or under Prof. P. Marti) in FE codes. This has already been accomplished in the case of the Cracked Membrane Model, which is available as user material for shell elements in ANSYS. Furthermore, as part of a Eurostars funded industry collaboration, we developed the Compatible Stress Field Method (CSFM), which enables the computational design and analysis of concrete structures in plane stress.
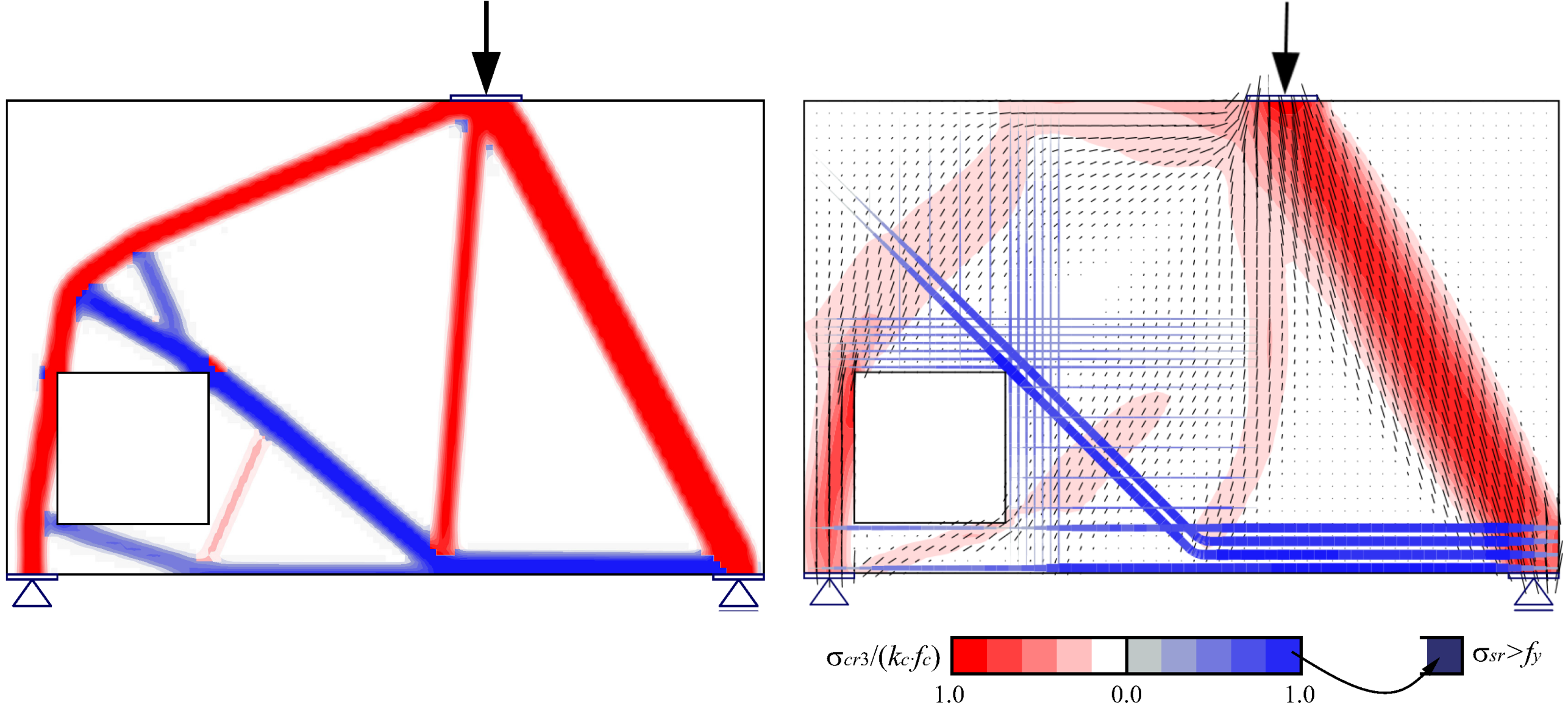
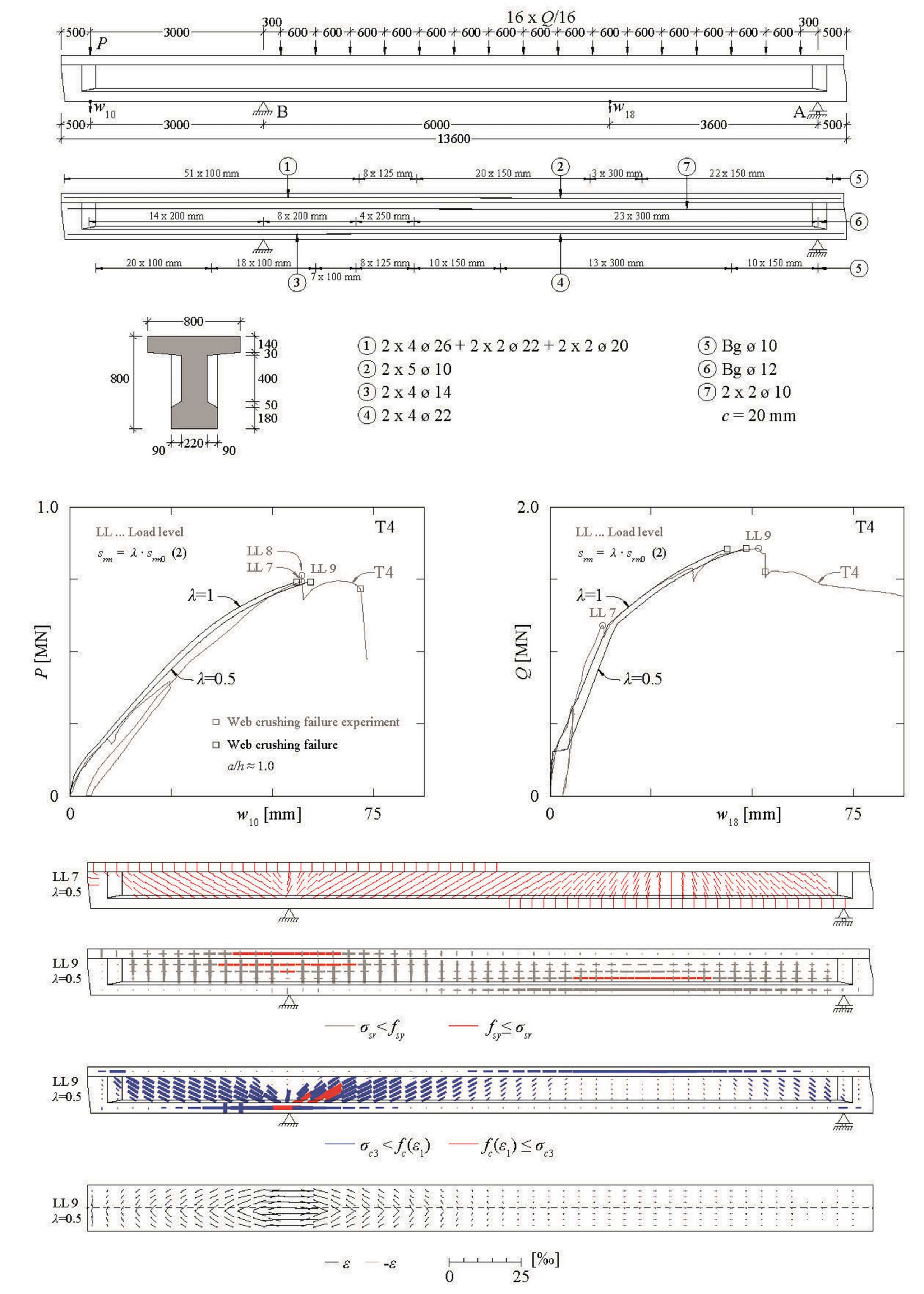